The Uses of Plasma Cleaning Prior To Wire Bonding
- Davide
- Jul 24, 2024
- 4 min read
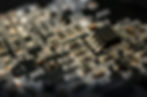
By understanding the mechanics and benefits of plasma cleaning, you can appreciate its role in enhancing the reliability and performance of wire-bonded semiconductor devices. This is crucial for advancing technology in many high-tech industries.
Through the effective removal of contaminants, plasma cleaning significantly boosts the reliability and performance of electronic components, making it a critical technology in the fabrication of semiconductor devices.
Plasma Cleaning and Wire Bonding
Wire bonding is a critical process in semiconductor device fabrication where thin wires, typically made of gold, aluminum, or copper, are used to create electrical connections between the integrated circuit (IC) or chip and its packaging. This connection is essential for the chip to communicate with other components or the larger system, such as a printed circuit board (PCB). Wire bonding must be highly reliable to ensure the overall performance and longevity of the electronic device.
Before wire bonding can take place, the surfaces where bonds will form—known as bonding pads—must be impeccably clean. Any contamination, whether organic, inorganic (such as oxides or fluorides), can significantly degrade the quality and strength of the wire bonds. Contaminants may come from various sources, including handling processes, storage conditions, and even the ambient air.
Plasma cleaning is employed to prepare these surfaces by removing these unwanted contaminants. This cleaning technique uses plasma—a state of matter similar to gas but with some of its particles ionized (charged)—to achieve effective cleaning. This is achieved through mechanisms such as ion sputtering, where ions in the plasma physically knock contaminants off the surface, and chemical reactions with radicals (highly reactive atoms or molecules) generated in the plasma that can break down contaminants.
Modes of Plasma Cleaning
There are two primary modes of plasma cleaning:
Direct Mode: In this method, the substrate (like IC chips and bonding pads) is exposed directly to the plasma, benefitting from ion sputtering, chemical reactions, and ultraviolet radiation from the plasma. This direct exposure ensures thorough cleaning but can be more aggressive.
Downstream Mode: Here, the substrate is not directly exposed to the plasma source but instead to the reactive species generated by the plasma. This method primarily relies on chemical reactions at the surface to clean it, which is generally gentler than the direct mode.
Benefits of Plasma Cleaning
The advantages of using plasma cleaning prior to wire bonding are substantial. It removes contaminants effectively and also enhances the adhesion of the wire bonds to the pads, which is critical for reliable electrical connections. Improved adhesion reduces problems such as non-stick-on-pad (NSOP) and bond lifting—both are common issues where the wire either does not stick properly to the pad or lifts off after bonding. By enhancing the cleanliness of the bonding pads, plasma cleaning greatly increases the yield of the manufacturing process and reduces the likelihood of bond failures.
Plasma cleaning can be customized to the specific needs of a manufacturing process, utilizing different gases (like argon, oxygen, or hydrogen) alone or in mixtures, and can be adjusted for the size and throughput of the production.
This cleaning technology is crucial in fields that demand high reliability in electronic components, such as in semiconductor manufacturing for consumer electronics and more stringent applications like space satellite instrumentation. In these environments, even minor imperfections can lead to significant failures, making the effective cleaning provided by plasma treatments invaluable.
Contaminants
The efficacy of plasma cleaning lies in its dual approach: physical cleaning through ion sputtering where impurities are physically knocked off the surface, and chemical cleaning where reactive radicals induce reactions that break down contaminants. This method is particularly valued in precision-dependent industries such as electronics and semiconductors for its effectiveness, efficiency, and the clean, residue-free results it offers.
The three primary types of contaminants in semiconductor and electronic manufacturing are organic, oxide, and fluoride contaminants, each impacting the manufacturing process in distinct ways.
Organic Contaminants
Organic contaminants typically originate from human handling, the use of packaging materials, adhesives, and fluxes during the manufacturing process. These substances often consist of oils, greases, and various hydrocarbons. Their presence is problematic as they can insulate electrical connections, impeding effective electrical contact. Furthermore, under the operational conditions of the device, these organic materials can degrade, generating harmful by-products that compromise device integrity and functionality.
Oxide Contaminants
Oxides form when metal surfaces interact with oxygen, either from the ambient air or during manufacturing processes. Common examples include silicon oxides or oxides of the metals used in chip construction. The formation of metal oxides on bonding pads can obstruct proper adhesion and electrical connectivity during the wire bonding process. This results in fragile bonds that are vulnerable to failure when exposed to thermal or mechanical stresses, posing a significant reliability concern.
Fluoride Contaminants
Fluoride contaminants often result from the utilization of fluorine-containing gases in various semiconductor fabrication processes, especially in etching and cleaning operations. These fluorides can react with metals, like aluminum found on bonding pads, forming stable compounds that are resistant to conventional cleaning methods. The presence of such compounds can severely impact the adhesion and electrical performance of the semiconductor devices, leading to diminished reliability and operational efficiency over time.
Final Thoughts
At SCI Automation, we take pride in our team of seasoned professionals who bring a wealth of experience and a track record of success in the industry. As pioneers and leaders, we are committed to developing innovative solutions tailored to the unique demands of the industry.Â
Our goal is to deliver customized solutions that address your specific needs and challenges. At SCI Automation, we see ourselves as your partners in achieving excellence. Should you have any questions or require assistance with plasma technologies, please feel free to contact our team for expert advice and support.