OUR FEATURED PRODUCTS
Is Vacuum Plasma Treatment Right for You?
Vacuum plasma treatment solutions are ideal for businesses that:

Require precise and efficient surface modification of materials, such as plastics, metals, ceramics, and textiles.

Seek a cost-effective and environmentally friendly alternative to traditional surface treatment methods.

Need to improve the performance and durability of their products, ensuring the highest quality and customer satisfaction.
Feeling defeated by your manufacturing challenges?

Relying on poor adhesion
Achieving good adhesion is crucial in various industrial applications, particularly in the semiconductor and automotive industries. These two sectors rely heavily on the integrity and performance of their products, making it essential to address adhesion challenges. Poor adhesion can lead to a multitude of problems which are typically found in the wire bonding, injection molding, and underfill manufacturing process steps. The problems include non-stick failures, low pull test results, delamination, hot spots during stress test and end product use, and ultimately premature failure of end products.
Non-stick failure during the wire bonding process
Poor adhesion between the wire and the bonding pad can result in non-stick failure, where the wire does not form a strong, reliable bond with the pad. This can lead to issues such as open circuits, signal degradation, and reduced device performance. Ensuring proper adhesion during the wire bonding process is essential for maintaining the electrical integrity of the semiconductor device.


Low pull test results
Low pull test results indicate weak bonds, which can be attributed to poor adhesion between the materials being tested. In the semiconductor industry, low pull test results can signal weak wire bonds or poor die attachment, leading to potential electrical instability or device failure. In the automotive industry, low pull test results can be a sign of weak adhesive or sealant bonds in various components, potentially compromising vehicle performance, durability, and safety. Ensuring good adhesion is critical for achieving satisfactory pull test results and maintaining the overall quality of products in both industries. This aspect be investigated by inspecting the bonds and check for intermetallic compounds formation during the wire bonding process.
Hot spots
Hot spots are localized areas of elevated temperature that can result from poor adhesion. In the semiconductor industry, inadequate heat dissipation due to poor adhesion between the die and heat sink can lead to hot spots on the device, which can cause thermal stress, device failure, or a reduction in performance. In the automotive industry, hot spots can occur in various components, such as engine parts, exhaust systems, or electrical connections. These hot spots can accelerate wear and tear, reduce component life, and even cause safety hazards, making t essential to ensure proper adhesion.


Premature failure of end products
Poor adhesion can lead to premature failure of end products in both the semiconductor and automotive industries. In semiconductors, poor adhesion between different layers or between the die and the packaging material can result in device malfunction, reduced performance, or complete failure. In the automotive industry, inadequate adhesion of coatings, adhesives, or sealants can cause components to wear out prematurely or fail, impacting vehicle performance and safety. Addressing adhesion issues is crucial to prevent these problems and ensure reliable end products.
What Is Plasma Cleaning?
Vacuum plasma cleaning is a process that involves the use of plasma generated in a vacuum chamber to clean and modify surfaces at a microscopic level.
This technique relies on the creation of a low-pressure environment and the introduction of an electric or radio frequency field to ionize a process gas (typically argon or oxygen). The resulting plasma contains a mix of charged particles, neutral atoms, and reactive species that interact with the surface, effectively removing contaminants and improving surface properties.
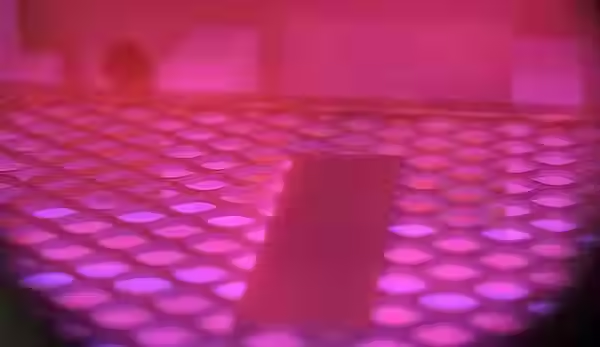
View inside a vacuum plasma chamber during a plasma cleaning process using argon.
The specific contaminants targeted by vacuum plasma cleaning include organic residues, particulates, and oxide layers. This process is particularly effective at removing these contaminants from lead frames, substrates, and semiconductor dies used in the semiconductor and automotive industries. Enhanced surface cleanliness and adhesion properties are crucial for ensuring high-quality bonding, improved electrical performance, and increased reliability of the end products.

Before Plasma
Hydrophobic surface weak surface interactions contact angle (water) 77.0°

After Vacuum Plasma Treatment
Hydrophilic surface strong surface interactions contact angle (water) 10.7°
Plasma Cleaning Vs. Alternatives
When comparing vacuum plasma cleaning to alternative cleaning methods such as wet cleaning, UV cleaning, and others, several benefits and drawbacks must be considered:

Wet cleaning, which typically involves the use of chemical solvents or detergents, can be effective in removing contaminants.
However, it may leave residue and moisture on the surfaces, leading to corrosion or poor adhesion.
Vacuum plasma cleaning avoids these issues, as it is a dry process with minimal environmental impact.
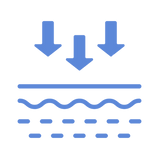
UV cleaning relies on the use of UV light to break down contaminants on surfaces. While effective in some applications, UV cleaning is limited to surface contaminants and may not be suitable for removing particles embedded in the material.
Vacuum plasma cleaning can reach embedded contaminants more effectively. Also some materials are sensitive to UV light and may be degrade during this process.

Other cleaning methods, such as mechanical polishing or brushing, can damage delicate surfaces or introduce new contaminants.
Vacuum plasma cleaning is a non-contact, non-abrasive method, making it well-suited for sensitive materials.
Work With SCI Plasma
SCI Plasma has been a pioneer in vacuum plasma cleaning and etching systems since 2000.
As a small company originally founded in Italy, we quickly grew and became an invaluable supplier for big players all over the world.
Our advanced vacuum plasma treatment technology is designed to optimize the performance, durability, and functionality of materials used in various industries. By using our solutions, you can enhance adhesion, increase surface energy, and achieve superior cleanliness for your materials.
The company headquarters have been set in Singapore since 2007 to better serve the Asia Pacific region where most of the semiconductor manufacturing takes place. The manufacturing facility has stayed for a long time in Singapore, but in 2019 relocated to Chennai, India.
Although our presence is mostly in Asia, our systems are scattered all over the world thanks to the support of our local partners.